Form and function collide in Nos Ailes, a 3D printed footwear company created with modern design and sustainability at its core.

Nader Alkhabbaz is a 23-year old New Jersey native and recent graduate from Princeton University with a Bachelor’s Degree in Architecture. But he’s not designing buildings. Instead, Alkhabbaz’s enthusiasm for fashion, computational design, and footwear inspired him to found Nos Ailes — a footwear company committed to changing the game.
“As a designer I want to push the future of footwear forward into a new era, an era filled with new computational and algorithmic possibilities and make people rethink what’s possible.”
– Nader Alkhabbaz, creator of Nos Ailes
Read on for a question and answer session with Alkhabbaz and insight into how Braskem’s Bio-Based 3D filament FL600EVA-BIO has helped bring his evolving vision to life.
The leap from architecture to shoes
What inspired you to begin printing footwear?
Having come from a formal architecture background, I felt like there still was something missing in terms of design direction in my life. I’ve always been passionate about footwear and I heard from several footwear designers how their transition from architecture to footwear was seamless. It intrigued me.
I’d become aware of a gap in the footwear design industry. My formal education exposed me to the parametric design possibilities for architecture, and I saw that these same tools could be applied to the world of shoe design. Nowadays with intuitive virtual reality tools and parametric modeling, the landscape of footwear design is completely evolving.
(Parametric design is a process where specific parameters are input into a design software tool; these parameters act as constraints while the design software generates an ideal structure or products based on the given parameters.)
Printing in 3D
Why did you decide to use 3D printing as your means for production?
The obvious benefits with 3D printing for footwear is the immediacy of bridging the 3D design logic into the real world; you can literally prototype and print your designs in the same day and iterate and improve upon it so much quicker. It also became clear early on that in order to bridge aesthetics and functionality, I’d have to work through additive manufacturing workflows.
Once certain that 3D printing was the correct prototype and manufacturing path, I was faced with learning the medium. As any seasoned 3D print user knows, there’s a learning curve associated with the art and science of 3D printing.

What were some of the biggest challenges you faced when starting?
The biggest challenge early on was learning to dial in settings and getting acclimated to 3D printing. I had to learn a lot about fine tuning certain design choices and 3D modeling techniques specifically for printed workflows. I also had to experiment with a range of material options, change up my designs many times, experiment on bridging complex forms with functionality, and more.
What was the reaction when you first began posting about your work?
The reactions were very polar. You had people complaining about the extremity of the designs and you equally had those who saw the future vision and respect that design curiosity. At the end of the day this is a community effort; nothing is ever done with one individual alone and I love the fact that more and more people can see what’s possible with printed footwear than ever before.
Deciding on materials and methods
What materials did you initially try and why?
I tried a lot of flexible filaments, and we did a lot of tests at DiveDesign where I participated in a computational design fellowship in the Summer of 2022. I always knew I wanted to work with Thermoplastic Polyurethane or Thermoplastic Elastomer (TPU/TPE) because of its natural low shore hardness and material feel, and durability was also a key in experimentation. We went through a range of options but of course the more flexible you want to go, the more design challenges you’ll have in getting them to print effectively.
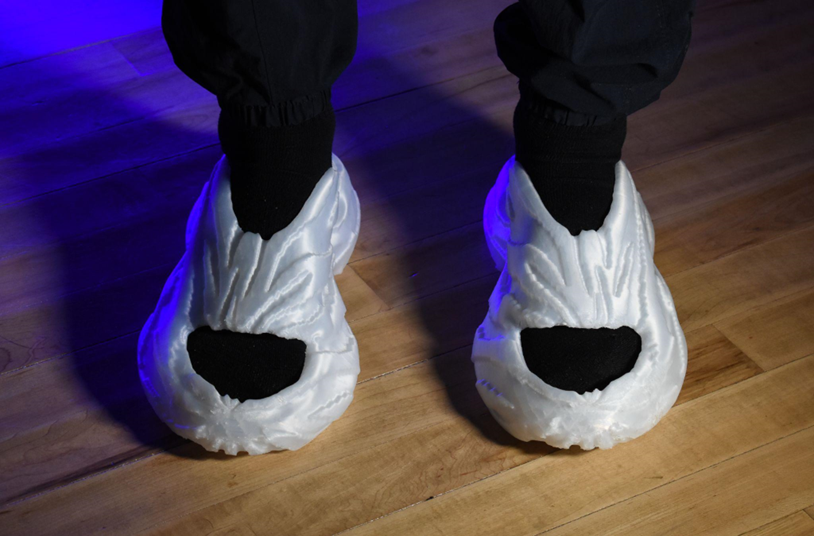
Printability issues and maintenance. The material often has to be printed very slowly or with much fine tuning, and post print clean-up is substantial. Additionally, filament options for footwear production are very limited, and oftentimes print speed and quality is difficult to improve significantly without higher end machinery.
After some experimentation with TPU’s, I was introduced to Xtellar's FL600EVA-BIO —a biopolymer EVA (ethylene vinyl acetate) flexible 3D filament. It’s part of an exciting lineup of revolutionary bio-based plastics made from raw sugar cane, promising a more eco-friendly alternative to more traditional flexible 3D printing materials.
When you first heard about Braskem’s new BioBased Flexible EVA, what was your initial reaction? What was intriguing about it?
I was super surprised to hear about an EVA filament for 3D printing applications. It got me thinking about the many footwear applications it can support. A bio-based filament is always intriguing when fulfilling that sustainable vision we have as designers. I’d heard of several applications of EVA that were done through the conventional molding process but never about a 3D printable filament so of course I wanted to learn more.
How important is the sustainability aspect to you and your customers?
Sustainability is essential; it has to be embedded into the production process. It’s vital to not only our business or smaller communities but also our existence to consider these design approaches.
How has the new Bio EVA compared to your TPU versions?
The Bio EVA is incredibly lightweight, I didn’t expect that at all! The material has a really nice frosted finish, almost a blend between clear and pearl white. Compared to other TPUs I’ve experimented with, it's more sustainable and definitely more lightweight.
In addition to its low density, Xtellar's FL600BIO-EVA filament is chemical and moisture resistant, and requires no drying time — meaning your design ideas can be made that much quicker. (To get started on your own creations, you can purchase the filament directly from Braskem’s website.)

Closing thoughts on Bio Eva and what excites you for the future of sustainable functional materials?
Sustainable functional materials are the future of the printing industry. The fact that we can work with a filament that’s sustainably sourced gives so much relief as designers.
What’s your vision for the future of Nos Ailes?
My vision is for Nos Ailes to be considered at the top of the footwear industry, pushing footwear forward into a new future that’s more seamlessly integrated with additive manufacturing and tailored to the consumer. Everyday I think about the quote from the late icon Virgil Ablog, “Young architects can change the world by not building buildings.” And I’m here to do just that.