What is the FL600EVA-BIO flexible filament?
FL600EVA-BIO is a flexible ethylene vinyl acetate (EVA) biopolymer filament. Biopolymers like FL600EVA-BIO provide a more sustainable alternative to traditional flexible 3D printing materials currently available on the market.
Xtellar's leading innovation in renewable and recyclable plastics; and has expanded the availability of sustainable materials for use in 3D printing applications such as automotive, aerospace, consumer, packaging, and industrial markets. The low carbon footprint formulation of FL600EVA-BIO is not only made from a renewable resource, but also delivers a comprehensive combination of enviable attributes for direct drive 3D printing systems:
- Flexibility
- Ductility
- Light-weighting
- Excellent surface finish
- Low warpage
- High dimensional stability
- Superior layer adhesion
One of the greatest attributes of Xtellar's FL600EVA-BIO is that it’s a flexible filament that requires no drying time — saving you countless extra hours.
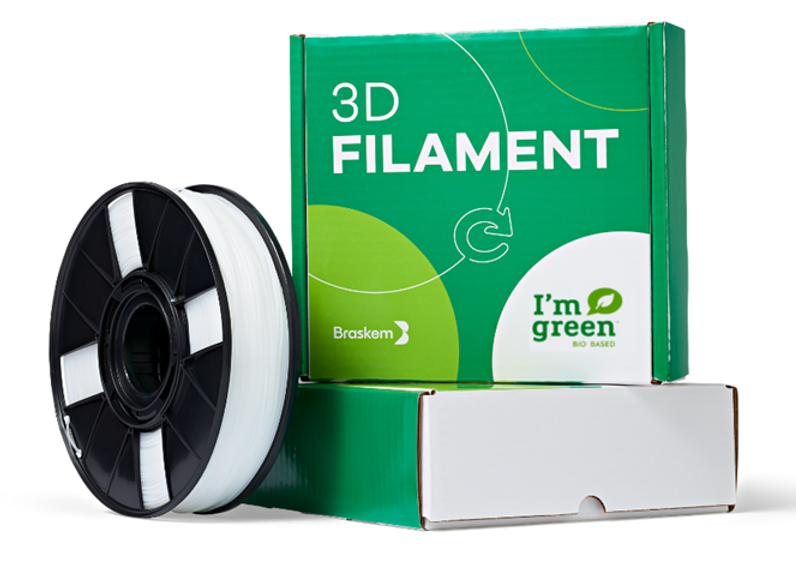
Beyond the obvious benefits of choosing earth-friendly print materials, using an EVA filament over TPU (thermoplastic polyurethane) in 3D flexible printing has its own list of substantial perks:
-
Low density: won’t weigh down your print
-
Chemical resistance: won’t break down on exposure to most chemicals
-
No moisture uptake: won’t cause a steam outbreak in your printer or warp your prints
Parts created from FL600EVA-BIO are both flexible and lightweight. And in addition to rapid prototyping and mass customization, it presents a sustainable option for 3D printing applications where EVA is customarily used in:
-
Shoes
-
Packaging
-
Fashion
-
Consumer products
-
Industrial applications
3D Printing Flexible Materials with a Direct Drive System
Sure, it’s possible to print with flexible materials on most desktop printers…but it’s not a great idea. This is because flexible materials are, well…flexible. They want to bend and curl as the extruder pulls them in. So it's best to use flexible printing materials in configurations where the extruder sits as close as possible to the hot-end. Therefore, a direct drive configuration is ideal as the gear which pulls the filament into the extruder sits directly above the hot-end. This direct drive print configuration also allows for faster print times, fewer failures, and an all-around better printing experience with flexibles. That’s a significant list of wins.
Extruder Gear Tension
Extruder gear tension: the amount of force pressing a filament against the extruder gear. For rigid materials, a higher tension helps to pull the filament into the hot-end without slipping — which can be a real problem. But for flexible materials like the FL600EVA-BIO, excessive tension can cause the filament to kink and get caught in the machine. So, we suggest the best practice of relaxing some of this tension by loosening the screw or spring that controls your printer's gear tension.
Fan Cooling
Fan cooling is essential to ensure each layer of printed material is cooled before the next is layed. When printing with FL600EVA-BIO, Braskem recommends setting the fan to 100% after the first layer is printed. Otherwise, lingering heat introduces the potential for your print to droop or even warp. Using plenty of cooling for your FL600EVA-BIO prints will ensure that each layer cools before it has time to deform or warp.
Bed adhesive
To best prepare your bed substrate, choose an EVA compatible adhesive. Braskem recommends glass bed substrates coated with polyolefin (PO) adhesive glue sticks for use with FL600EVA-BIO.
Infill Type
When printing with this material, it's best to avoid infill strategies that zig zag or have otherwise very sharp turns, or that alternate deposition patterns between layers. Instead, for stellar results stick with infill patterns such as grid, concentric, or triangles. Additionally, avoid patterns with excessive retraction.
Ready to Start Printing with Braskem’s FL600EVA-BIO?
This filament is currently available in a neutral color and with two diameters to choose from — 1.75mm and 2.85mm.
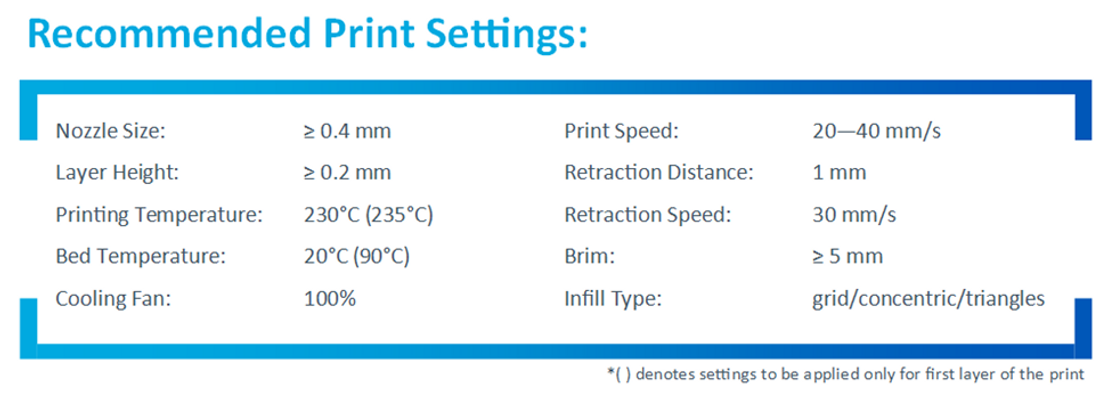
To ensure quick success, as a starting point be sure to follow the guidelines outlined above as well as the Braskem-recommended print settings depicted in the graphic above. But as always, do keep in mind that every printer and brand is slightly different, so be sure to tune your settings to what works best on your own setup.