Close your eyes for a minute and imagine it’s November in Alaska, you’re outside lounging in your favorite plastic chair while enjoying a snow storm (totally reasonable). And you’re thinking to yourself: “Man, I'm so grateful this cozy plastic chair was made with materials strong enough to withstand these subfreezing temperatures. If my favorite plastic chair suddenly shattered and deposited me onto this quickly rising blanket of snow, it would really put me in a mood. I mean, not only would my favorite chair be gone, but I don’t really like watching snow storms from the ground.” We’ve all been there (work with us here), but we probably don’t know what keeps our favorite plastic chairs thriving in the snow.
Now, if you did a little Googling, you’d learn that materials like polypropylene are responsible for keeping plastic chairs strong and supportive in cold, harsh environments. And more specifically, it's the low glass transition temperature of materials like polypropylene — or PP for short — that keeps everything from ice cream containers to car bumpers from shattering at below freezing temperatures. Now, if only someone could figure out a way to 3D print this material? Well look no further than Braskem, a global leader in 3D materials, they have finally figured out how to harness this unique power of PP’s low glass transition temperature and deliver the ultimate 3D printing solutions for cold temperature applications.
As your freezing bum might attest to in the above scenario, material selection for use in harsh environments is critical. If a material is not formulated correctly for the conditions of its desired use, a catastrophe may ensue. This presents significant challenges for industries looking for additive manufacturing material solutions for cold-temperature applications. This also presents a challenge for 3D print users looking to do the same. With a wide range of easy-to-print polypropylenes, Braskem is here to help.
First, let’s talk more about glass transition temperature.
When it comes to cold environments, glass transition (Tg) temperature is generally described as the temperature at which molecular chains of a given material transform their behavior— and this transformation has some serious implications. It causes the molecular chains to go from being mobile above the Tg (the material will bend or dent when enough force is applied), to being fixed and often brittle when below the Tg (the material will shatter when enough force is applied). When assessing a material for cold applications, glass transition temperature is a key indicator of its potential performance — as it tells you how well you can expect a material to perform in cold conditions.
With a variety of Braskem polypropylene options available, let’s take a closer look at FL900PP-CF, a carbon fiber reinforced polypropylene filament for 3D printing applications. Made utilizing 100% recycled carbon fiber, this formulation provides a unique balance of dimensional stability, toughness, and light weighting, all without sacrificing printability. Braskem’s approach to carbon fiber incorporation into a custom formulated polypropylene base resin has resulted in a breakthrough for the 3D industry. In a bit we will look at how that combo stacked up against other formulations, but for now, here’s a spoiler alert: the use of carbon fiber increased overall cold temperature toughness significantly when compared to the others.
Next, testing for toughness.
Braskem’s carbon fiber reinforced polypropylene was tested for impact toughness at subzero temperatures according to ASTM D3763 — a standard method of testing high speed puncture properties of a material. In other words, the test determines how much force it will take to punch a hole through the material in question.
The impact tests were conducted at three different temperatures: 23C, 0C, and -20C. Test results were recorded with an average standard deviation of 2.4%, which means the “spread” of all test results stayed remarkably close to the mean (average overall) result. Translation: the results of the test are consistent and reliable.
When subjected to testing, Braskem’s carbon fiber PP performed like a champion — retaining up to 99% of impact toughness at subzero temperatures when compared to 23 degrees C/73 degrees F. This means you won’t see a decline in material performance should the temperature drop from a balmy room temperature to VERY VERY cold. Bingo!

Results are in – carbon fiber reinforced PP for the win!
Alright, now let’s compare Braskem’s carbon fiber reinforced FL900PP-CF polypropylene to with three other commonly used materials for additive manufacturing:
● ABS+CF (Acrylonitrile Butadiene Styrene reinforced with Carbon Fiber)
● PLA (Polylactic Acid)
● Nylon
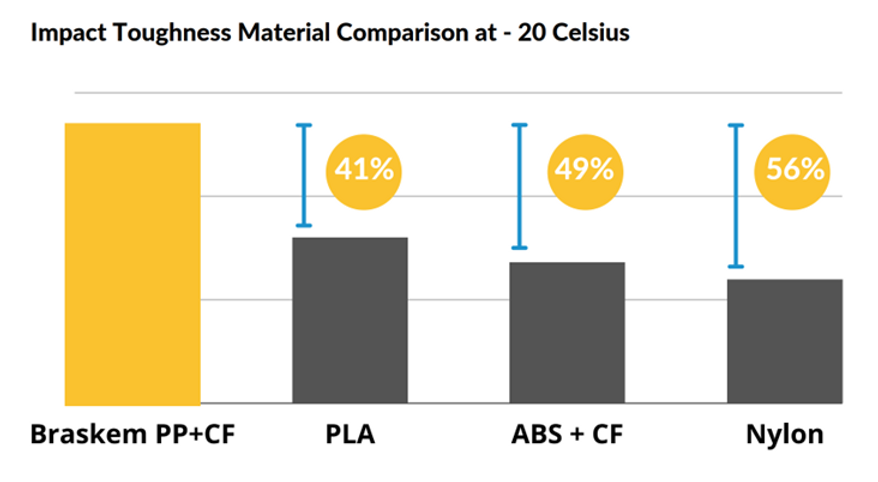
When tested under the same conditions as the FL900PP-CF, these materials came up woefully short. As shown in the diagram below, Braskem carbon fiber polypropylene outperformed its competitors by at least 41%. This is a tremendous difference in performance that could make or break the success of a particular part in a cold temperature application.
While this article zeroed in on the superior cold temperature impact performance of Braskem’s carbon fiber reinforced polypropylene, the addition of its end-use surface finish right off the printer and low density, make it the clear choice for 3D printing for cold temperature applications. Whether in the lab, out in the field, or for end use parts that need to look good while still taking a beating, the FL900PP-CF will go the distance.